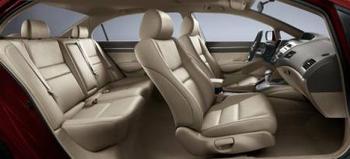
车内空气质量问题日益受到车主关注,但国人对车内空气质量的重视程度还不够,主要是看重内饰的颜色好看,造型漂亮或做工精细。对材料环保与否以及车内空气中含有的有毒成分了解不深,这点将导致汽车车内空气对乘客身体健康造成影响。本文将对目前一些企业采用的车内环保材料及技术进行概述。
丰田RAV4内饰采用Softex皮革材料
天然动物皮革经常用于豪华轿车的内饰材料中,不过由于其成本高昂以及动物保护协会的反对,其在汽车中的应用受到了限制。
目前,丰田RAV4和普锐斯V中采用了Softex新型人造皮革,其良好的冷却性能被用于汽车座椅的表面材料。与真皮材料相比,无论采用穿孔还是
缝合线工艺,甚至是触摸感上都极其相似。除了在需要大面积发泡和颗粒化部分不能采用这种材料外,其他部位均能够利用其代替真皮材料。
Softex是一种热塑性聚氨酯,其具有高透气性和高散热性的特点。它具有良好散热性的原因是这类材料能够反射空气中的红外线,这是其本身固有的属性,并没有经过表面处理。在测试中,Softex材料在相同环境温度下比其他材料表面温度低10℃。不同颜色的Softex材质在热性能上有细微差别,不过即使是吸热性能较强的深色系材料也比其他人工皮革材料的散热性佳。
布料和乙烯基材料仍然是应用最普遍的基础座椅材料,尤其是在非豪华车上。而乙烯基材料在炎热、潮湿的天气条件下,乘客出汗后其衣物会与座椅靠背粘在一起。这是由于乙烯基属于无孔材质,它不会“呼吸”。另外,乙烯基材料受到阳光暴晒会发生干裂,甚至真皮材料长时间暴露于阳光下也会发生细微开裂,特别是枕垫处。
大部分较新的人造皮革在一定程度上具有“呼吸”功能,不过其程度与真皮相比相差甚远。不过,Softex人造皮革材料的水分吸收速率比天然皮革慢15%,但释放速度却更快,这使乘客的背部感到更加舒适。
虽然Softex材料于乙烯基材料释放水分的速度都很快,但不同于乙烯基材料的是,前者不会因为受到阳光暴晒而发生干裂。此外,相比天然皮革材料,Softrex材料在焊缝疲劳、磨损和抓挠测试中表现均优于天然皮革。另外,Softex材料通过了丰田的耐久性实验。
在抗张强度方面,Softex材料略逊于天然皮革一筹,在表面修剪和缝制花纹时或许会受到限制。在吸收灰尘颗粒方面,Softex与其他人造皮革相同,清洗起来比天然皮革更方便。
东丽开发出使用植物材料纤维的汽车内装部件
东丽近日开发出利用来源于植物的材料PLA(聚乳酸)纤维“ECODEAR”的汽车内装部件,并且在全球首先开始正式生产。
ECODEAR是以玉米为原料的纤维。聚乳酸在土壤等自然环境中最终被分解为二氧化碳和水的生物分解性纤维,燃烧热量也低。
该公司面向丰田汽车从5月12日开始发售的新型“Raum”的备用轮胎盖和地毯供应了该部件。备用轮胎盖采用了在PLA纤维中均匀混合天然纤维红麻(Kenaf)并进行热压整形处理的硬质板,为100%来源于植物的产品。
“今后将在需要减轻环境负担的汽车相关部件的开发上,增加适用于车门、轮圈、车座、天棚材料以及Line Mat等其他汽车内装部件的PLA纤维产品的产品线”。
HEXPOL公司开发Dryflex AM热塑性弹性体汽车脚垫材料
HEXPOL公司旗下Elasto业务部近日开发出一系列热塑性弹性体(thermoplastic elastomers,TPES)材料,主要应用于汽车脚垫。
Dryflex AM材料基于弹性体(SBS)与热塑性弹性体(SEBS),它兼备橡胶的耐磨性以及塑料的可加工性,利用肖氏硬度测量法,在标准条件下将标准的压针压入标准试样的表面,考察压入的深度来衡量试样的硬度,得到的结果为肖氏硬度A值在50-75之间。
Dryflex AM材料的应用范围包括汽车脚垫、硬币垫以及内饰材料中。汽车脚垫材料需要具备高耐磨性以及耐刮擦性,另外还要具备良好的防滑性,特别是在潮湿环境下。Dryflex AM材料表面具有较高的摩擦系数,满足防滑要求。
随着世界各国政府制定的燃效以及碳排放法规,汽车制造商们正在寻求进一步促使汽车轻量化的方法。热塑性弹性体材料汽车脚垫比传统的汽车脚垫材料要轻得多。此外,与其他脚垫材料不同的是,Dryflex AM材料仅含有极少的刺激性气味,无需经过硫化并且该材料能够100%回收利用。这些特质简化了生产成本,提升了效率。
汉高针对汽车电子系统推出新有机硅导电胶提升耐温性和抗震性
随着汽车电气系统的结构、工作环境的日趋复杂,其中相关材料性能也必须得到相应提升,汽车传感器材料需要有个更强的抗震性、耐温性。汉高近日开发出一款全新的有机硅导电胶(ECA),能够应对复杂、恶劣的系统环境。ICP 4000系列导电胶能够承受200℃的高温,此外能够承受强烈的振动。
导电胶是一种固化或干燥后具有一定导电性能的胶黏剂,它通常以基体树脂和导电填料即导电粒子为主要组成成分,通过基体树脂的粘接作用把导电粒子结合在一起,形成导电通路,实现被粘材料的导电连接。由于导电胶的基体树脂是一种胶黏剂,可以选择适宜的固化温度进行粘接,同时,由于电子元件的小型化、微型化及印刷电路板的高密度化和高度集成化的迅速发展,而导电胶可以制成浆料,实现很高的线分辨率。传统的导电胶采用环氧树脂材料用于特定的传感器上。随着技术进步,电气系统中的热量和振动源越来越多,传统材料已经无法满足这些要求。
ICP 4000有机硅导电胶在温度为175℃,湿度为85%,3000次-40℃-175℃的热冲击的实验环境下经过3000小时的测试后,不论在单次循环或长期运行方面其表现均良好。
各类汽车电子厂商都有着不同的生产和应用要求,ICP4000导电胶在高温高振动环境下的抗电阻性、附着力、导热性和灵活性均能满足正常工作需求。该导电胶的导电填料采用银填充,基体树脂采用可热固化的硅树脂。比起传统环氧树脂材料它具有更好的灵活性,能够自动补偿热膨胀系数不匹配现象,因此在极端的高振动情况下它依旧能够正常工作。另外,在ICP4000导电胶固化过程中释放出的刺激气体和残留胶体非常少,不会影响到周边传感器的正常工作。
锦湖日丽开发塑可净™汽车内饰用超低VOC材料保证车内清新空气
车内空气质量的不达标很大程度上源自于内饰用材料的不合格,锦湖日丽专门针对汽车中挥发性有机化合物(VOC)的散发问题而开发出超低VOC材料——塑可净™,它不但可以满足汽车内饰的耐候、耐热、抗冲击等性能要求,更有效控制了有机挥发物的生成与析出,其最大亮点是超低的散发性。
锦湖日丽依托中韩方母公司锦湖石化和日之升强大的聚合技术背景,有效降低原料聚合过程中残留单体,低分子的齐聚物的析出,并凭借10多年的改性经验,整合了聚合、反应挤出、设备工艺方面的国际专家成立专题研发团队,投入经费1500多万元,历时3年,成功开创了国际领先的PSS技术,通过聚合、萃取、以及后加工后的净化等一系列复杂环节有效降低了车内VOC含量。从第三方检测报告的数据看,塑可净 TMABS的散发性可以达到TVOC﹤18μgC/g的水平,塑可净TMPC/ABS的散发性可以达到TVOC﹤15μgC/g的水平,比目前市场上的主流内饰材料的散发性降低60%,远低于各主机厂的管控标准,也远低于目前最严格的沃尔沃汽车的TVOC﹤30μgC/g的管控标准。
超低VOC塑可净™系列产品真正从源头上有效改善了汽车车内空气质量,给消费者一个健康、安全的驾乘环境。
粘胶剂选择
除了材料以外,材料粘胶剂的选择也对车内空气质量有着至关重要的作用。汽车内部装饰大多数使用人造革、聚氨酯泡沫塑料、塑料壁纸、乳胶海绵、人造地毯、布、丝绒和木材等材料,增加车内美观。例如顶蓬、地毯、门板、仪表盘等。
目前在国内汽车内饰大多还是使用易燃、有毒、污染环境的溶剂型胶粘剂,如氯丁胶胶粘剂。溶剂型胶粘剂不仅造成资源严重浪费,严重污染环境,而且对施工人员的健康造成很大威胁。使用溶剂型胶粘剂装饰的汽车,在很长一段时间内溶剂不断地缓慢释放出来,使司乘人员受到伤害,汽车质量也受到影响。而水基胶粘剂由于以水为溶剂,不含有毒溶剂,甚至可以做到挥发性有机物几乎为0。因此近年来在汽车工业上,水基胶粘剂正在取代传统的溶剂型粘合剂,开始用于汽车内饰,并且增长速度很快。目前世界上汽车顶棚内衬水性胶粘剂的比例已超过1/3。以日本汽车为例,目前汽车内饰胶几乎全部实现水性化。今后水基聚氨酯胶粘剂的年增长估计保持在8%-10%。
目前在汽车内饰用水基聚氨酯粘合剂研制方面,美国、日本和西欧走在前列。我国水基聚氨酯粘合剂的应用和研究尚处于起步阶段,研究开发工作虽十分活跃,但应用水平不高,生产厂家不多,且品种单一,产品也多为低档产品,在性能方面与Bayer等公司还有较大差距。特别是高档水性聚氨酯胶粘剂全部为进口产品,主要来自Bayer公司、罗门哈斯公司、日本DIC公司等。我国大陆的水系聚氨酯粘合剂的开发与生产都还处于起步阶段。